Hydroforming – a technology with many advantages
Hydroforming is a process technology that will give the development engineer new unique possibilities to develop and design complex components in pipes and sheet metal.
The hydroforming process gives the component minimal material thinning and high accuracy with small tolerances, because the fluid pressure perpendicular towards the material during the whole process.
One of the cost-effective advantages that the hydroforming process gives, is that one component is finished in one operation could replace several different components. This will remove the assembly process of several parts.
To optimize the material, use and scrap rate, different components could be combined in the same pipe and tool, and then be separated by cutting. This will give the product less scrap, shorter cycle times and lower tooling cost.
TM Tube Systems have installed hydroforming capacity to manufacture everything from serial production to prototypes in the most common material, like stainless steel and aluminum. In production we have the latest generation of hydroforming machines with a press force of 20.000kN. In our prototype shop we have 2 hydroforming machines with a press force of 5.000kN and 6.000kN, these are used for prototypes and low volume production.
Benefits of hydroforming
Complex products
- Design freedom for development engineers
- The product cross section could be varied
- Possible to get Air gap between two pipes
Component accuracy
- Minimized material thickness
- Minimized spring back
- Small Tolerances
Cost efficiency
- One product replaces several components
- Optimal material use
- Flexible tools with lower tooling cost
- Space effective equipment (2×5 m)
Our hydroforming history
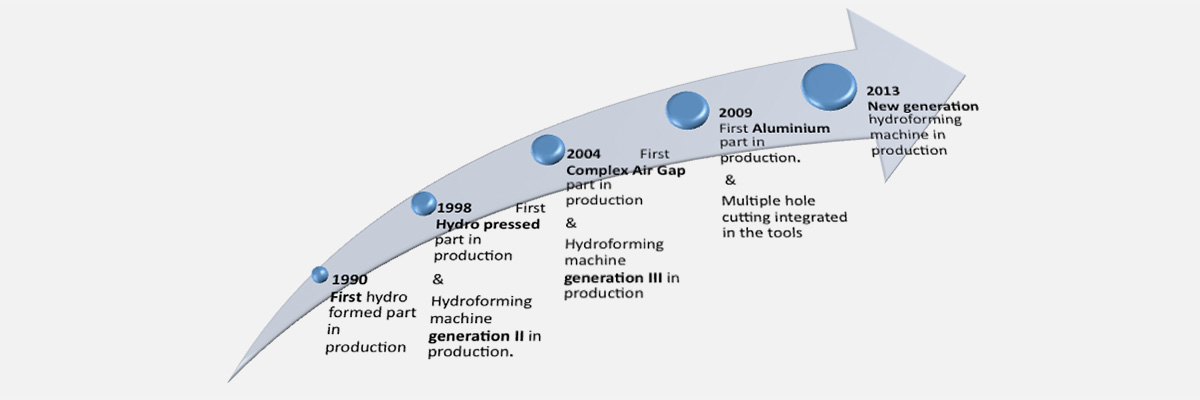